제1장 보관일반론 및 거점시설
1)보관의 정의: 물품의 생산과 소비의 거리를 조정하여 시간적 효용을 창출하는 활동
2)보관의 10가지 원칙:
①통로대면 보관의 원칙 (입,출고를 용이하게 하고 창고내 레이아웃의 기본원칙)
②높이 쌓기의 원칙 (창고 용적효율 향상)
③선입선출의 원칙 (Life Cycle의 최소화)
※선입선출이 필요 품목
- 상품형식 변경이 잦은 것 / - 상품수명주기가 짧은 것 / - 파손·감모가 생기기 쉬운 것
④회전대응보관의 원칙 (물품회전율 빈도수에 따라 구분)
⑤동일성·유사성의 원칙(관리효율, 생산성향상)
⑥중량특성의 원칙 (대형,중량물 - 하층 / 소형, 경량물 - 상층)
⑦형상특성의 원칙 (표준품은 랙에 보관하고 비표준품은 별도 보관)
⑧위치표시의 원칙(단순화 - 소인화 - 효율화)
⑨명료성의 원칙 (식별표시로 신입사원 실수 최소화)
⑩네트워크 보관의 원칙(계통적으로 관련화-그룹화): 관련품목을 한 장소에 모아서 보관
*보관물품의 흐름방식
-one Way 방식: 입고와 출고가 별도로 설치, 물품이 일방통행으로 이동
-U Turn 방식: 입출고구가 동일, 또는 동일한 쪽, 물품이 입고방향과 반대방향으로 출고.
*창고의 기능: 저장/ 수급조정/ 가격조정/ 총수송비 절감/ 연결/ 매매기관적/ 유통가공
3)보관품목의 배치
- ABC 관리방법: 중요도에 따라 차별적으로 관리하는 재고관리방식
① A그룹 - 품목은 적고 보관량과 회전수는 많다. 정기발주시스템
② B그룹 - 품목, 보관량, 회전수가 중간정도이다. 정량발주시스템
③ C그룹 - 품목은 많고 보관량과 회전수는 적다. Tow bin시스템 또는 JIT방식
- ABC 분석
① 품목별로 수량 또는 매출액을 산출한다.
② ABC분석표에 수량 또는 금액이 큰 순서대로 기입한다.
③ 품목순으로 수량 또는 매출액의 백분율을 기입한다.
④ 누계백분율을 기입한다.
⑤ 각 품목을 가로축(X축)에 놓고 수량 또는 매출액의 백분율을 세로축(Y축)에 놓아 막대 그래프를 만든다.
⑥ 각 품목별 누계백분율을 세로축에 놓고 각 점을 선으로 잇는다. 이선이 파레토 곡선이다.
⑦ 끝으로 이들을 분류기준에 따라 ABC 3등급으로 분류한다.
*ABC 분석표
분 류
|
매출액
|
재고 품목수
|
연간 총사용금액
|
적정재고관리기법
|
A 품목
|
크다
|
10 ~ 20%
|
70 ~ 80%
|
정기발주법
|
B 품목
|
중간
|
20 ~ 40%
|
20%
|
정량발주법
|
C 품목
|
작다
|
40 ~ 60%
|
5 ~ 10%
|
Tow-Bin법
|
*ABC분석에 의한 품목배치
① 입출고가 동일 장소인 경우 - 입출고구 근처부터 A품목, B품목, C품목의 순으로 배치. (가장 우수함)
② 입출고가 다른 장소인 경우 - 입출하의 긴급도 및 우선도가 높은 순서로 배치하되 출하우선으로 배치하고,
출고구 가까운 쪽에 회전이 높은 그룹을 배치.
즉 출고구로부터 A, B, C순으로 배치
*보관의 주요형상 구분
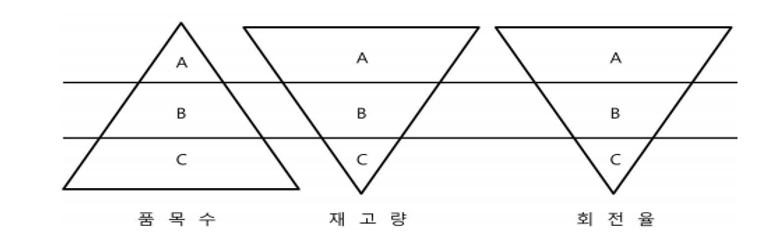
** 보관용 하역시스템 : 재고보관점수(Item수), 보란량, 회전수별로 ABC군으로 분류하여 조합
- 파렛트 보관
❶ A-A-A : 품목수는 적지만 수량이 많고 회전율이 높은 물품으로 맥주, 청량음료, 시멘트 등 입출고가 빠른 물품, 보관설비는 플로우랙
❷ A-A-C : 대량재고를 갖고 있으면서 별로 이동을 하지 않는 불량제품이나 계절변동형 제품으로 보관점수는 상대적으로 적으며
파렛트의 수동적재가 유리하고 유니트형 랙이나 플로우랙은 불리
❸ A-C-A : 회전수만 높고 보관량이 적은 중간공정이나 임시출고라인에서 피킹을 실시하는 제품
❹ A-C-C : 점수, 보관량, 회전수가 모두 적어 파렛트를 직접 쌓는 형태로 파렛트랙을 중심으로 한 보관기기는 포크만 부착되어 있으면
가능한 보관형식
❺ B-B-B : 보관수량, 및 회전수가 모두 보통이라 설비가 간단하고 레이아웃의 변경도 용이
❻ C-A-A : 보관점수가 많고 회전수가 많아 관리가 복잡한 형태
❼ C-A-C : 재고점수 및 재고량은 많지만 회전수가 적어 고층랙에스태커크레인을 이용하는 것이유리
❽ C-C-A : 보관점수는 많지만 보관량이 적고 제품의 이동이 많은 형태로 고층랙시스템을 이용하여 보관이 가능,
적층(Mezzanine)랙 이용이 좋다.
❾ C-C-C : 재고량, 제품의 이동이 모두 적지만 점수가 많아 관리가 어려워 파렛트에 직접 쌓는 것이 유리
*보관용 하역시스템: 재고보관점수(Item수), 보란량, 회전수별로 ABC군으로 분류하여 조합
- 파렛트 보관
A-A-A
|
품목수는 적지만 수량이 많고 회전율이 높은 물품
맥주, 청량음료, 시멘트 등 입출고가 빠른 물품, 보관설비는 플로우랙
|
A-A-C
|
대량재고를 갖고 있으면서 별로 이동을 하지 않는 불량제품이나 계절변동형 제품으로
보관점수는 상대적으로 적으며 파렛트의 수동적재가 유리하고 유니트형 랙이나 플로우랙은 불리
|
C-A-A
|
보관점수가 많고 회전수가 많아 관리가 복잡한 형태
|
C-C-A
|
보관점수는 많지만 보관량이 적고 제품의 이동이 많은 형태로
고층랙시스템을 이용하여 보관이 가능, 적층(Mezzanine)랙 이용
|
*창고의 분류
①구조에 따른 분류: 보통창고, 기계화창고, 자동화 창고
②기존 화물유통촉진법에 따른 분류
-제1종창고: 일반창고(보통창고, 저장창고, 야적창고, 수면창고)
냉동. 냉장 창고 – 온도가 낮아질수록 알파벳은 커지고 숫자는 작아진다
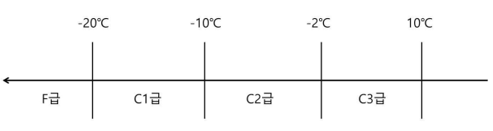
-제2종창고 (위험물 창고)
③기능에 의한 분류 : 저장창고, 보세창고, 유통창고
④운영형태에 의한 분류 : 자가창고, 영업창고, 보세창고, 공공창고
*창고의 종류에 따른 보관비용
①영업창고: 상당규모의 보관서비스를 고정적으로 필요 시, 자가창고운영보다 비경제적임.
②리스창고: 초기투자비가 그리 크지 않고 작업비용이 상대적으로 높은 비중,
전체 보관 비용에서 가변비용이 중요한 구성요소
③자가창고: 총비용비중 고정비가 상당부분 차지
④자동자가창고: 고정비가 아주 높고 인력의존도가 낮기 때문에 가변비용은 아주 낮다.
단위처리량당 비용이 아주 낮은 장점
*창고의 위치결정
①창고입지 다섯가지 요인- P(화물,제품), Q(수량), R(경로), S(서비스), T(시간)
②P-Q분석: 화물이 어느 정도의 양으로 흐르고 있는가에 대한 물류유형 분석기법.
물의 범위에 속하는 분석요소 (품종, 포장, 단위수량, 단위용적)
양의 범위에 속하는 분석요소 (중량, 개수, 용적, 시간, 건수)
③R분석: 어떠한 물량이 어떠한 경로로 흐르고 있는가를 과거에서부터 현재까지 파악
④S-T분석: 주부문인 제조와 판매부문을 효율성 있게 하기 위해 보조부문이 어떠한 기능을
갖추어야 하는지를 과거와 현재의 실상을 면밀히 분석 후 결정하는 기법.
*자가창고와 영업용 창고의 장단점 비교
구 분
|
자 가 창 고
|
영 업 창 고
|
장점
|
자사에 적합한 창고 설계
기계화에 의한 생력화 실현
높은 시설 이용도로 비용 절감
공간용도 변경 및 특화 보관소 구성 가능
자사에 적합한 운영 방식(적정서비스 유지)
입출고 시간 유연성 높음
작업시간에 대한 탄력성이 높음
창고운영에 대한 노하우 축적이 가능
입지선정의 폭이 넓음
|
필요로 하는 스페이스를 언제, 어디서든지 이용가능
전문업자로서 전문적관리운용
설비투자가 불필요
보상제도의 확립
비용지출의 명확화
|
단점
|
막대한 창고 건설자금 소요
높은 고정비용 발생(원금상환, 이자지급)
인력배치 및 기기설비
보관능력의 확장성 부족
한번 구축 시 증설과 감소가 용이하지 않음
보관량 증가에 따라 로스도 증가
재고품의 관리가 소홀해질 우려
입지변경은 용이하지 않음
|
시설변경의 탄력성이 적다.
토탈시스템과의 연결이 약하다.
치밀한 고객서비스가 어렵다.
자사목적에 맞는 창고설계가 어렵다.
|
*창고의 공간관리: 창고의 레이아웃을 고려 시 스페이스의 활용과 창고작업이 용이한 것을 중심
① 입체적으로 쌓도록 한다. (상부공간 활용)
② 창고설비를 최적화하여 공간을 활용 (드라이브인 랙, 모빌랙)
③ 통로면적을 가급적 줄인다.
④ 계획적으로 공간을 활용하여 불필요공간을 배제한다.
⑤ 융통성을 발휘하여 공간을 절약 (프리로케이션 시스템 채택)
⑥ 구분방법을 바꾸어 충진효율을 향상시킨다.
*창고내 레이아웃의 기본원리
① 물품, 통로, 운반기기 및 사람 등의 흐름방향에 있어 항상 직진성에 중점을 두어야한다.
② 물품, 운반기기 및 사람의 역행교차는 피해야 한다.
③ 물품의 취급횟수를 줄여야 한다.
④ 물의 흐름과정에서 높낮이 차이의 크기와 횟수를 감소시켜야 한다.
⑤ 화차, 운반기기, 랙, 통로입구 및 기둥간격의 모듈화
*트럭도크 소요수에 대한 풀이방법
※ 트럭도크 소요수 = 연간 트럭출입대수☓1일 대당 작업시간 / 연간 작업시간 ☓ 안전계수
(예제)연간 트럭출입대수7,000대 안전계수25%
1일대당 작업시간2.5시간 연간 작업시간 2,080시간
7,000☓2.5/2,080 ☓ 1.25 = 10.5 (약11개가 필요)
*창고의 집중 및 분산배치
|
특징
|
장점
|
단점
|
쌍
자
분
산
형
|
각 창고의 성격이 같은 형태로
창고 간에 품종구성이 같다.
고객과 가까운 거리에 크기가
비교적 작은 창고가 위치하여
고객서비스에 유리
|
한곳에서 모든 품목의 집화가능
고객과의 거리가 가까워
고객서비스에 유리
긴급한 출고에 대한 신속대응 가능
집중형에 비해 창고크기가
작기 때문에
창고내 운반거리가 짧다.
|
기계화와 생력화가 곤란
관리요원의 과다로 효율성 저하
재고와 현품과의 대응관계가 나쁘다.
집중형에 비해 재고량이
많지 않으면 품절손실이 증가
생산공정에서 각창고까지
운송거리증가
|
친
자
분
산형
|
각 창고간의 성격이 다른 형태로
보관품종도 다르다.
유니트화에 용이하지만
주문시 여러창고에서 집화해야함.
|
창고내 품종이 적어 관리가 쉬움
설비기능의 단순화로 경제적임
생산공정에서 창고까지 운송거리 단축
|
수요발생시 여러창고에서 집화해야 함
고객과의 거리가 멈
납품에 시간이 걸려 서비스 저하.
|
집
중
형
|
|
관리공간이 한곳에 집중돼 있어
정보와 현품대응 용이
수요에 대한 품목, 수량을 모두 구비
배송센터규모의 출하시설 운영이 가능
관리요원이 적어 효율성 제고
|
창고가 대형화로 인해
창고내 운반거리 증가
작업자 개인의 책임추적이 곤란
|
'물류관리사 관련 정보 나눔 > 4)보관하역론' 카테고리의 다른 글
제 6장 하역 장비 (0) | 2024.05.09 |
---|---|
제 5장 자동분류시스템 (0) | 2024.05.09 |
제 4장 하역론 (1) | 2024.04.29 |
제 3장 재고관리 (1) | 2024.04.18 |
제 2장 보세구역 (3) | 2024.04.01 |